Panasonic’s Electric Works Company Aims At Deeper Penetration In India
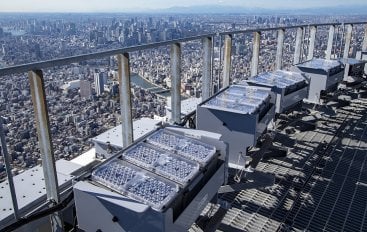
The National Stadium of Tokyo, that was the venue for the inauguration of the 2020 Tokyo Olympics (eventually held in 2021due to Covid), boasted unique lighting features. The 1,300 stadium lights were controlled in such a way that despite the brightness of stadium, the glare did not disturb the sportspersons. And the focus of the lighting could be changed depending upon whether it was a track event or a field event. The task of installing the stadium lights was done by Panasonic’s Electric Works Company, that won the Japan Lighting Award in 2022 for the lighting work.
Similarly, The Electric Works company is at the core of lighting overhaul that was carried out at Tokyo’s tallest structure, 634m tall Skytree dominating the city’s sky line. Using 2,362 lighting fixtures, using LED lighting, doing visibility checks from as far as 19 km and careful placement and design of each lighting fixture, the company, through its expertise developed over years, helped develop lighting that makes the tower visible from 20km away, while ensuring non-dazzling environment.
At the same time, it’s instrumental in lighting entire townships like Fujisawa Sustainable Smart Town, where technology is used extensively for energy self-sufficiency and efficiency.
It's not just in Japan that Panasonic’s Electric Works Company is lighting homes, offices and public landmarks. With 1 trillion yen worth sales in FY 2022 (Rs 62,500 crore), Panasonic has global presence too. The electrical products are sold in 109 countries, with 16 affiliated companies. In India, it is expanding its business in association with Anchor, in which it bought 80 per cent stake in 2007. It has four manufacturing units – Haridwar, Daman, Gujarat and Sri City in Andhra Pradesh, which started operating in April 2022.
Kiyoshi Otaki, Executive Vice President, Panasonic Corporation President, Electric Works Company, says, “Among our priorities, India holds a special place. As the world's most populous country with remarkable economic growth, we aspire to expand our operations and contribute to the Indian society. In the future, we will actively pursue exports and investments from India to Africa.
Toshinobu Kawasaki, Joint Managing Director, Panasonic Electric Works India (PEWIN), Panasonic Life Solutions India, says, “Panasonic's roots lie in the electrical materials market, with our very first product being a socket. Our goal in India is to enhance the quality of life by offering high-quality, cost-effective electrical construction materials (ECM) products. These offerings are a result of transferring advanced product and manufacturing technologies from Japan to our Indian counterpart, Anchor.”
Regarding the company’s targets for India for the next five years, he says, “Looking ahead to the next five years, our ambition in India is to significantly strengthen our market presence, particularly in the wiring device business. By 2030, we are targeting a 50 per cent market share in this segment. Additionally, we are focused on expanding our foothold in core businesses, including switchgear and lighting. Our strategy revolves around leveraging our technological expertise and market understanding to capture a larger portion of these segments, demonstrating our commitment to growth and leadership in the Indian electrical industry.”
Market demand
Growing urbanisation, construction boom and increasing awareness about lifestyle products as also energy efficiency implies that there is huge market for wires and cables, lights, switches and fans.
According to a report by EY Parthenon in November 2023, titled ‘Ascending Trajectory: Unveiling the Swift Growth of the Building Products Market in India’, “Electricals is the second largest segment in the building products market with growth driven by government schemes, a growing push for energy efficiency and increasing access to electricity in rural areas at affordable rates.”
In 2022, it came to 6.8 billion USD, and is slated to go up to 11.7 billion USD by 2028, according to the report. Among the leading players in the electrical segment, besides Anchor by Panasonic are Havells, Bajaj Electricals, Crompton Greaves, Jaquar, Finolex Cables, Norysis and Usha, each with market capture in dedicated areas.
Environment impact
While lifestyle and wellbeing are two important considerations in consumer decisions today, carbon footprint is an equally important plank and consumers are sensitive about the environmental impact of choices they are making. Regarding the environmental consideration of Electric Works products, Ryo Matsumoto, General Manager, Business Planning Department, Electrical Construction Materials Business Unit, Electrical Construction Materials & Living Energy Business Division, Electric Works Company, says, “Our focus extends beyond just offering high-quality products; we aim to enhance overall well-being by presenting comprehensive spatial solutions and promoting energy-efficient lifestyles. This is achieved through our diverse array of electrical equipment, designed to integrate seamlessly into various living spaces. Our commitment is to deliver not only superior quality but also holistic solutions that contribute positively to the quality of life and environmental sustainability.”
Talking about actual measures being taken, Toshinobu Kawasaki says, “Panasonic is actively working towards the ambitious goal of achieving net zero emissions by 2030. A significant step in this direction is the installation of solar panels across all our manufacturing plants in India. Additionally, we are meticulously measuring the electricity consumption of each piece of equipment to identify areas for improvement. By progressively replacing these with more energy-efficient alternatives, we are effectively reducing our carbon footprint.”
Manpower challenge
With automation taking over manufacturing, the manpower requirements have also evolved in every sector.
Kentaro Kobayashi, Vice President of Manufacturing, PEWIN, Panasonic Life Solutions India, says, “The focus now is on roles that support high productivity through automation. This includes expertise in high-precision component manufacturing, as well as the development and maintenance of sophisticated equipment.” He adds, “The key skill areas that are in high demand include mold development and maintenance, injection molding, metal press operation, and the development and upkeep of manufacturing equipment. These areas require highly skilled professionals, underscoring our commitment to maintaining top-tier production standards in an increasingly automated manufacturing landscape.”
He describes the multifaceted approach for availability of trained manpower. “We recruit graduates from specialised schools and experienced professionals, followed by comprehensive in-house training.” In India, the issue of trained manpower is solved through:
a. Bringing highly skilled personnel from Japan to provide training in India,
b. Sending select Indian employees to Japan for intensive training,
c. Leveraging the expertise of experienced local senior workers to mentor younger employees, and
d. Encouraging participation in Panasonic skills competitions to foster professional growth.
The company also collaborates with specialised skills schools and training institutions to attract and hire talented individuals. It also runs skill schools in Haridwar for training the local graduates to efficient workers.
Retention strategy
Getting quality manpower is just one part of the challenge. Retaining the manpower poses further challenge. As Kobayashi says, “One of our primary challenges in manpower management is the time-intensive nature of developing advanced skills. There's a significant investment in nurturing these skills within our workforce, and when skilled employees resign soon after their development, it represents a considerable loss for the company.”
Among the various strategies for retention that the company has evolved is wellbeing measures and Kobayashi explains, “Our commitment to employee well-being is evident through superior welfare systems, such as providing day-care centres and health-care rooms. These facilities not only support our staff's needs but also play a significant role in retaining personnel. By creating a supportive and growth-oriented environment, we ensure a steady availability of trained manpower for our operations in India.”
Technology transfer
Yet another challenge was the disparity in manufacturing infrastructure. Kobayashi shares, “Following the acquisition of Anchor, we found that the existing manufacturing infrastructure and operations did not meet Panasonic's global standards. Addressing this involved a concerted effort in skill development and production technology enhancement, in collaboration with our counterparts in Japan. This process included deploying automation and transferring technology within the Indian plant.” He adds, “Through regular personnel exchanges between Japan and India, we shared technology and skills, significantly strengthening our workforce and establishing the high-quality production system we have today.”