Contract Pharma- Drug Manufacturing, The Neglected Sector
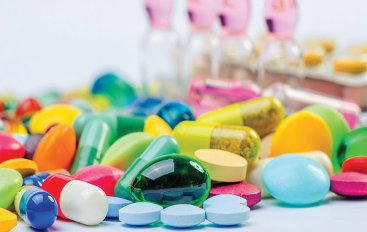
Contract Manufacturing Organisations (CMO) sector in CDMO (Contract Development & Manufacturing Organisations) occupies an important space in India. It has several inherent strengths, which can be leveraged to put India on top of global Active Pharmaceutical Ingredient (API) sourcing. At the commencement of the Covid-19 pandemic, it dawned upon the government and pharmaceutical stakeholders that India is overwhelmingly dependent upon China as a key supplier to the drug building block that is API, the therapeutic component of the medicine. This sequel on contract pharma focuses on leveraging upon drug manufacturing.
Due to Covid-19 induced disruption, the government introduced a Productivity Linked Incentive (PLI) scheme towards enhancing the domestic supply of 53 imported APIs, which fundamentally are the raw materials for essential lifesaving antibiotics. It has also announced the establishment of three API Parks to boost manufacturing.
For these 53 APIs, technologies are available in India. Today, funds are also forthcoming. Referring to a recent news report, PE are likely to invest nearly 3-4 billion USDs in Indian API companies over the coming year. Since the prices of major drugs, especially antibiotics are controlled, there is little incentive for backward integration or setting up of greenfield projects in antibiotics API due to the huge cost involved and poor returns. 25 years back, India used to be self-sufficient in antibiotics but cheaper imports from China led to the closing several plants including Indian Antibiotics Limited plant at Pune. For a quick comparison, as part of Europe’s reshoring efforts, Austrian government has offered to Novartis one third the cost of expansion & modernization of its plant producing amoxicillin antibiotic.
However, beyond antibiotics, there is a huge field of APIs, which is not covered by PLI and can be profitably exploited.
It would come as a surprise to many Indians who constantly read about India’s dependence on China to learn that we are the world leaders in API technology. As reported by the Chinese government English daily The Global Times, many Chinese manufacturers appreciate the capabilities of the Indian industry. Together, India and China contribute to 21 percent of the global API market. Many APIs are sent from China to India for final processing. There is a cooperative partnership between manufacturers in both countries in exporting drugs to the Western world. A Chinese Manufacturer has accepted that competing with India on production cost would be tough, as unlike production of table and chairs, in API production India has advanced production lines. The same article later called “India-the world’s largest API maker.” It was a reflection not of our large-scale plants but the technical depth and width allowing us to produce the widest range of products.
China is only ahead of us in antibiotic production due to the large-scale fermentation plants producing APIs at a much lower cost (among other reasons). China produces high-volume, low-cost APIs while India specialises in low-volume high-value APIs.
Indian CMO companies have huge strength in peptides, oncology and other potent APIs. Divis’s Laboratories operates the world’s largest single site API plant at Vizag. The Indian facilities have the flexibility to produce ranging from low-volume in grams for clinical research to hundreds of tonnes for commercial production. Many of these specialisations have high entry barriers for competitors to enter, even China.
If we look at the profile of API entrepreneurs, we find that many of them have Ph.D.s in organic chemistry or are chemical engineers. Even Dr. Anji Reddy, founder of Dr. Reddy’s Laboratory was a Ph.D. from National Chemical Laboratory (NCL) and started his career by synthesizing an API, which was being imported. Not only did he succeed but also improved the imported product. Another interesting aspect of Indian CMOs is their high profitability margins from 25-35% and they are largely debt free.
Take the Drug Master Files (DMF) filing in the US as a benchmark of API technological superiority. DMF are technical dossiers on API, which are filed with regulatory authorities and any application for approval of novel drug or its generic copy must be supported by DMF. According to Pharma Compass, India is consistently filing up to 50% of the total DMF filed with the USFDA much ahead of USA and China.
If we look at the DMF filed by top companies in following tables, we see that a majority of companies are from India.
Besides substantial cost advantage, a major advantage in outsourcing to India is its globally competitive manufacturing facilities and abundant talent. Usually, Indian CMOs instal state-of-the-art equipment. Sai Life Sciences, for example, has a 100% successful track record in regulatory inspections both from the US and Japanese regulatory authorities and works with 7 of the top 10 global pharma companies. Amsal Chem, a SME in Gujarat is the world’s largest manufacturer of isoniazid API (anti-malarial) and has 50% market share. Other companies like GVK Bio and Piramal Pharma Solutions etc. have a consistent track record in terms of commercial delivery.
One Indian company, Aarti Industries, which also operates in the API segment ranks among world’s top three companies in chlorination, top 2 players in ammonolysis and hydrogenation and among top 4 players in nitration technologies. There are several companies of equal repute in India. CMOs can play a big part in vaulting India among global biopharmaceuticals manufacturing destinations.
The drawback of the PLI scheme is its limited approach of only looking at import substitution rather than capturing a large global market share. We estimate that, with full support to the CMO sector, it is possible to scale up the global supply of API alone to $60 billion as merchant export by 2030, two times of present industry estimates. Spurred by the pandemic, as more countries commence indigenisation of formulations production, they will need to source API from two vital sources, India and China. Drug production, beside API also requires other imported ingredients such as excipients, dyes etc. Vaccine production alone requires 273 imported ingredients. Therefore, the government, in consultation with the industry should come up with a holistic policy for the development of CMO sector. Not only, it will elevate indigenous R&D as well as manufacturing output but augment the SME sector.